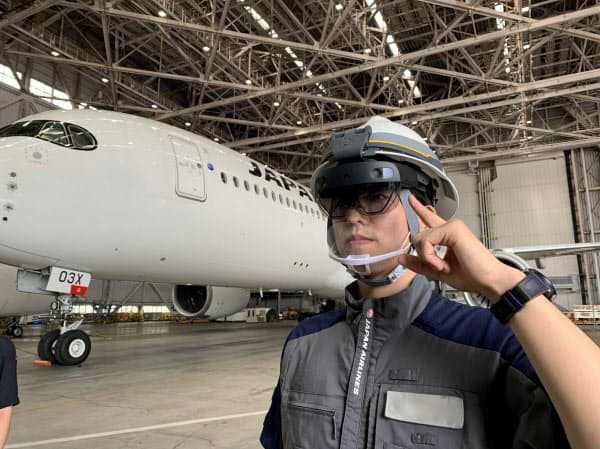
INDEX
- With the cooperation of the in-house venture team, the project was put into operation less than two months after launch.
- Remote social studies field trip made possible by staff enthusiasm
- A surprise flight simulator that caused a big stir
- Providing even more satisfying experiences for customers through remote work
"Enjoy a factory tour from home!! Remote social studies tour" was held on June 28, 2020. This project started in early May.
Abe: "Microsoft Japan, with whom we already had a connection, approached us and asked, 'In these times, why not hold factory tours online?' We decided to hold the suspended factory tours remotely using the online meeting system 'Microsoft Teams' and the mixed reality device 'HoloLens 2.'"
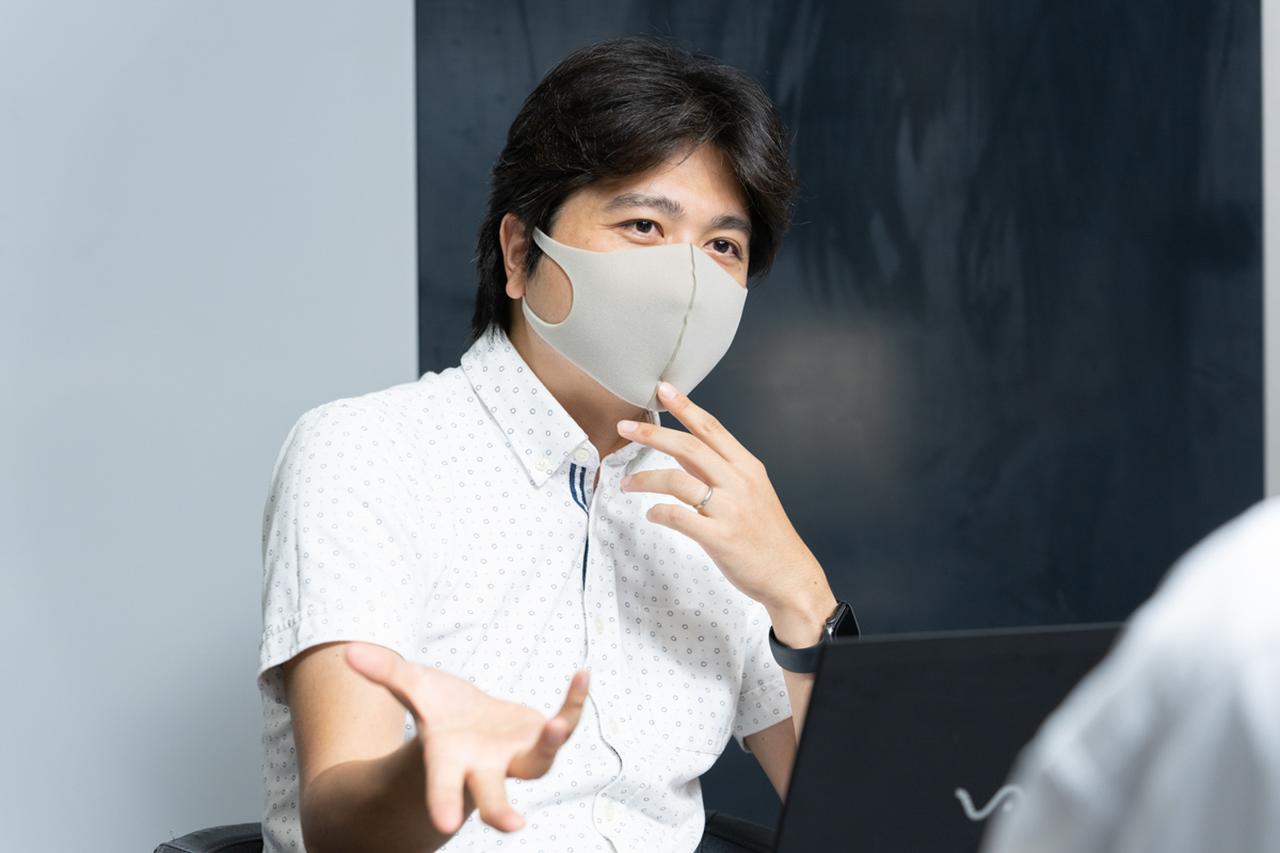
Abe Motohisa of the Revenue Management Promotion Department, who was in charge of planning, looks back on the project this way. As flight cuts continued due to the effects of the COVID-19 pandemic, it was a time when JAL was searching for something it could do. That's when Abe reached out to W-PIT, an in-house venture team officially recognized by JAL. Taniuchi Toru, a member of the team who works in the JAL Engineering Technology Department and is responsible for data analysis at the Maintenance Headquarters, looks back on the project.
With the cooperation of the in-house venture team, the project was put into operation less than two months after launch.
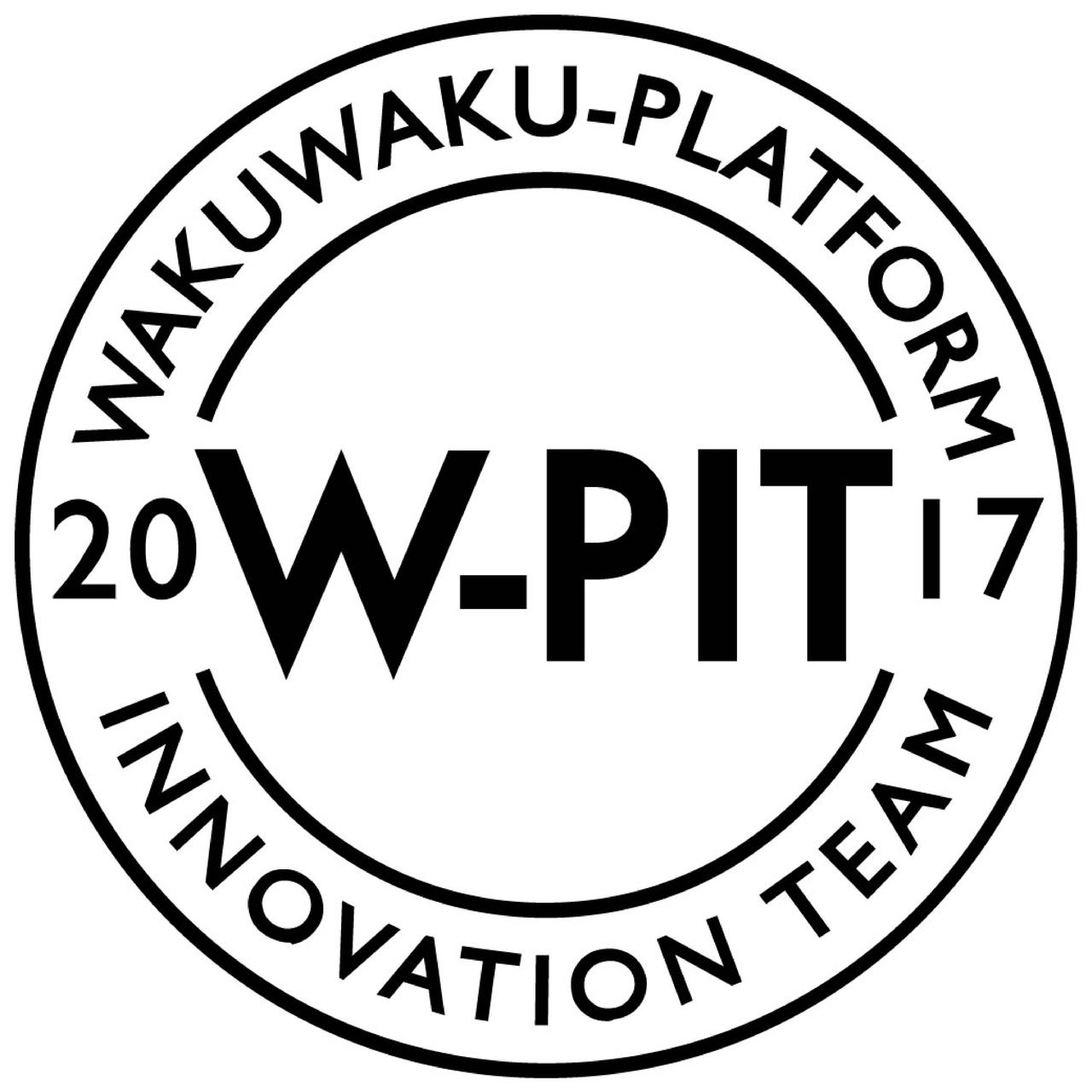
Taniuchi: "W-PIT is an abbreviation for Wakuwaku-Platform Innovation Team. It is an activity guideline based on the concept of excitement, which is to challenge the creation of new value through collaboration with different industries. This time, we collaborated with Microsoft Japan to try to provide new value, which matched our aspirations."
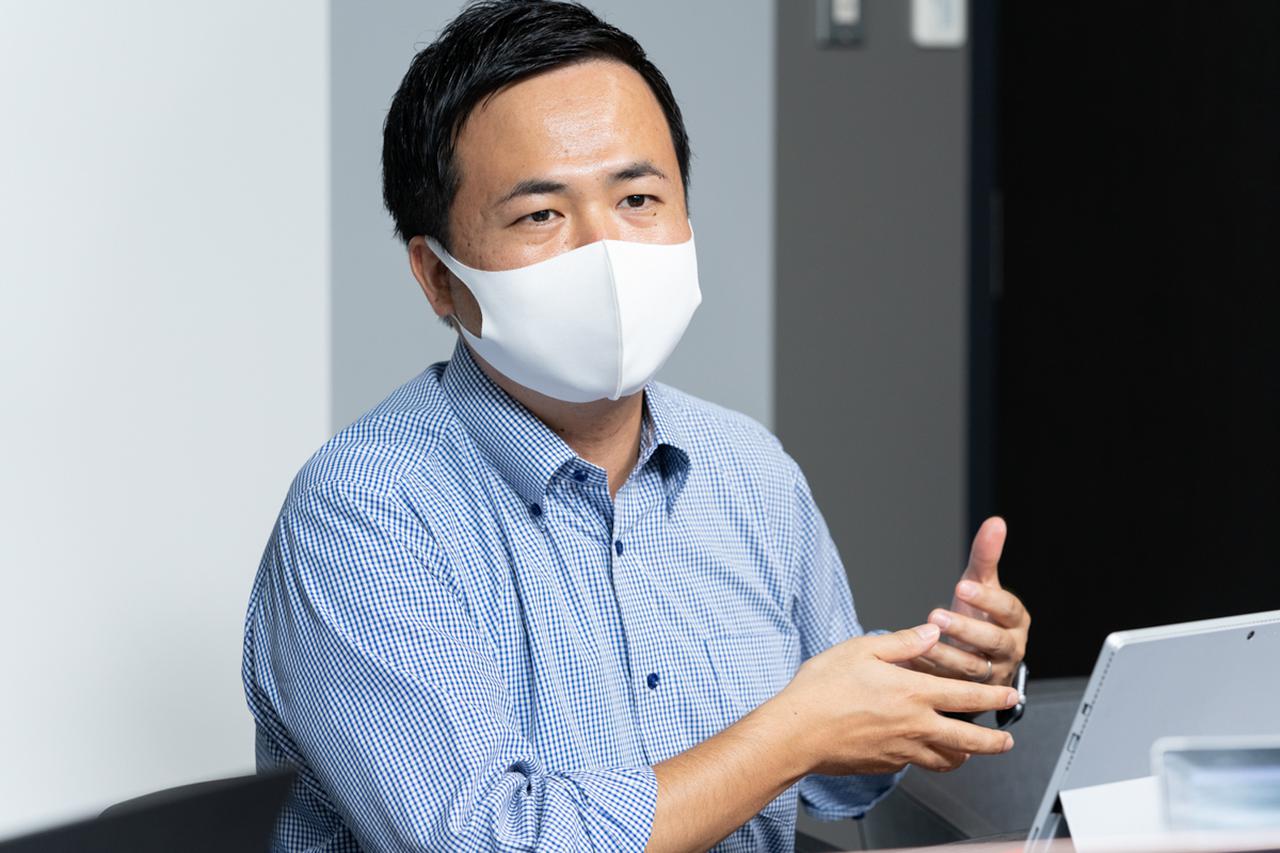
Emi Oe, a member of the W-PIT Cabin Education and Training Department and leader of this project, was also one of those who supported the plan.
Oe: "We had to propose a plan at W-PIT by a show of hands, and we thought we should definitely do this. I'm usually in charge of cabin training. I accompanied the team to select the location, filmed the simulator where I work, and acted as the host on the day."
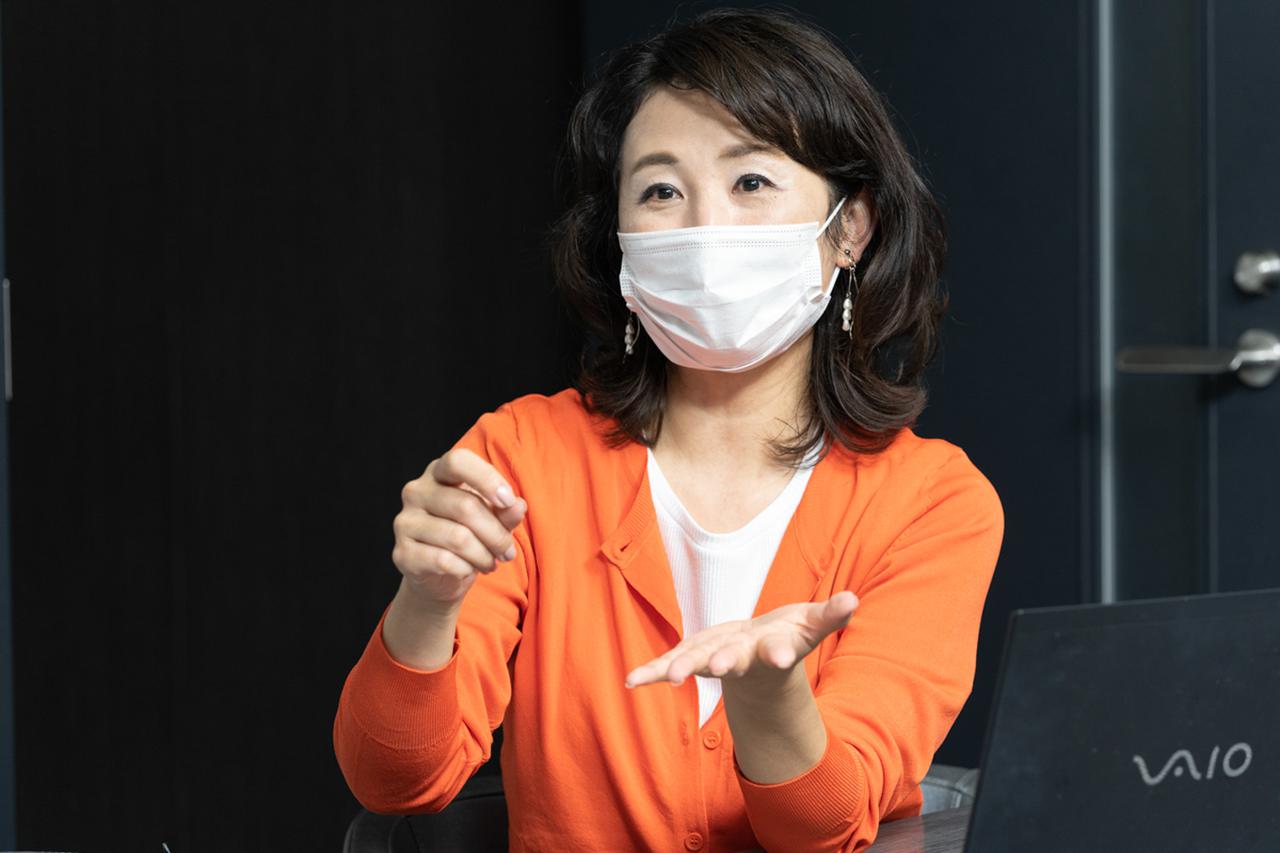
Thus, the project was launched, but it took just under two months to go ahead. It was the first attempt to remotely broadcast a factory tour of a maintenance yard. There were many hurdles to overcome. Although it was expected that making these adjustments would be a difficult road, there was a lot of positive feedback from within the company.
Taniuchi: "We had the PR department, the maintenance headquarters, and the department in charge of factory tours, so we got them all involved. Everyone was generally positive, and we quickly gained more and more friends."
Remote social studies field trip made possible by staff enthusiasm
One of the key features of the project is a gadget called "HoloLens 2." This device allows you to experience mixed reality, and can overlay virtual images on the scene in front of you in real time. Since customers cannot get close to the planes during an actual maintenance yard tour, the mechanics wear "HoloLens 2." While communicating with the female guide, they explain how the plane looks from the mechanic's point of view.
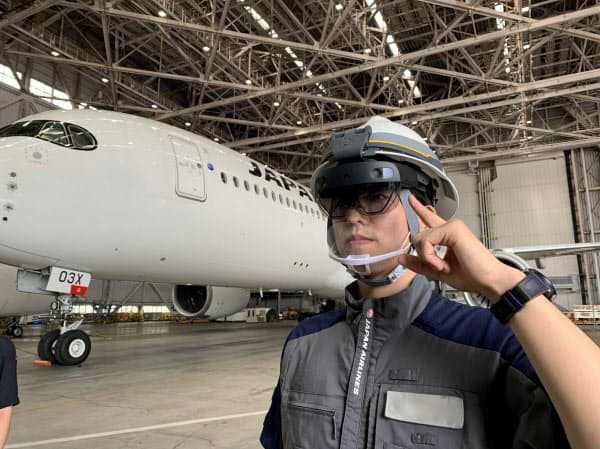
Taniuchi: "We had prepared various methods for distribution, but on the day itself, we realized that there were technical hurdles to overcome in streaming HoloLens 2 video in real time."
Because there was a possibility of image distortion occurring when streaming remotely, and to ensure that customers had the best possible experience, the decision was made to stream an information video recorded just before the event, rather than a live stream. This was a decision made by those on the ground in order to provide the best possible hospitality to customers.
The aircraft we arranged for the commentary was also a result of the team's efforts. It was the Airbus A350, the latest large aircraft introduced by JAL in 2019.
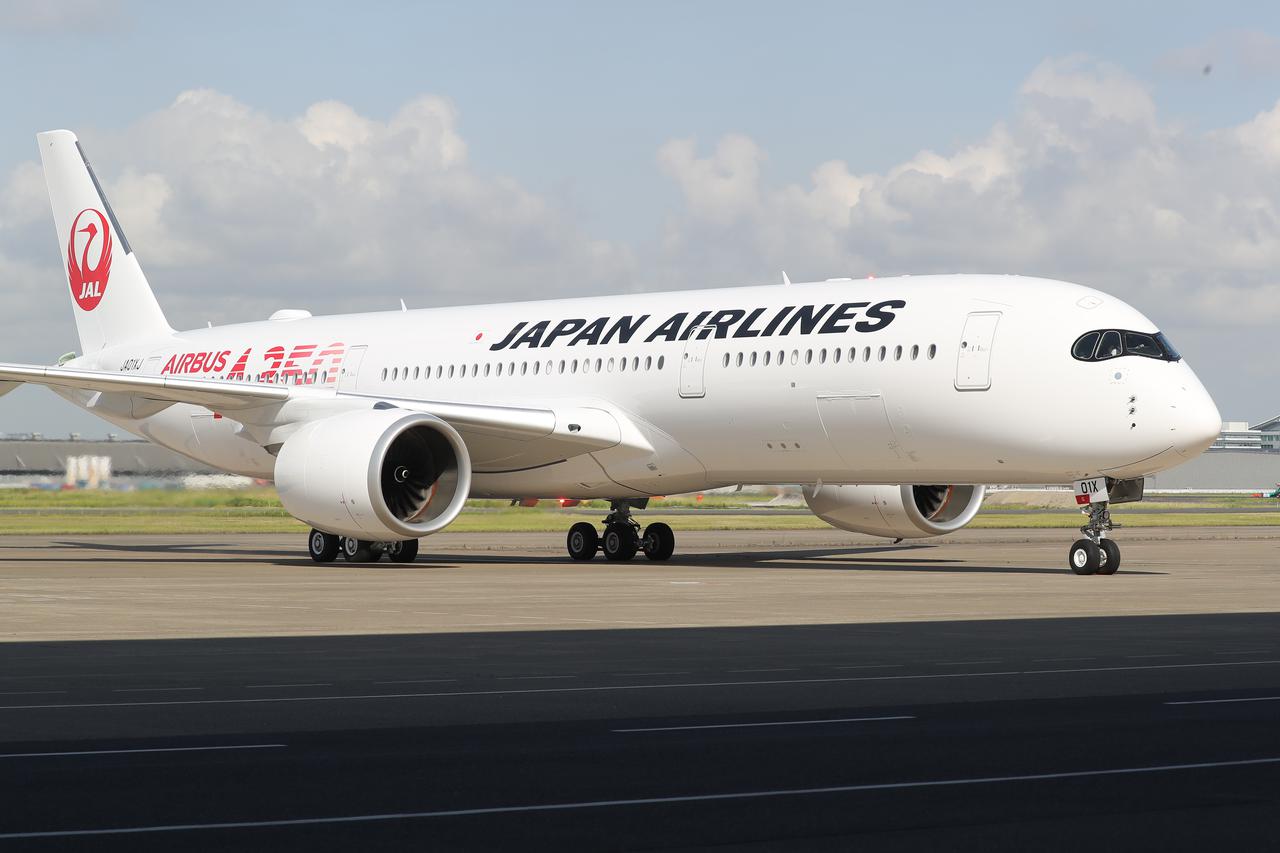
Taniuchi: "We had to make sure that the aircraft was safe and that there would be no problems with maintenance, so we had no choice. But if the aircraft used in the rehearsal was different, it would have been difficult to stage the show. So the PR department worked hard and we were able to secure the latest A350, which happened to be available."
Abe: "We were able to achieve something that would normally be difficult, and it really boosted the motivation of the staff. I think it was a great play."
A surprise flight simulator that caused a big stir
And so the broadcast finally began. First, host Oe gave a greeting and then gave a tour of the maintenance yard.
Oe: "We started by calling the staff on standby at the maintenance workshop from the studio, connecting the live broadcast, and then we walked around the back of the aircraft. When we got to the tip of the aircraft, a mechanic wearing a HoloLens appeared and played a video explaining the aircraft. It was my first time doing this, so I was very nervous."
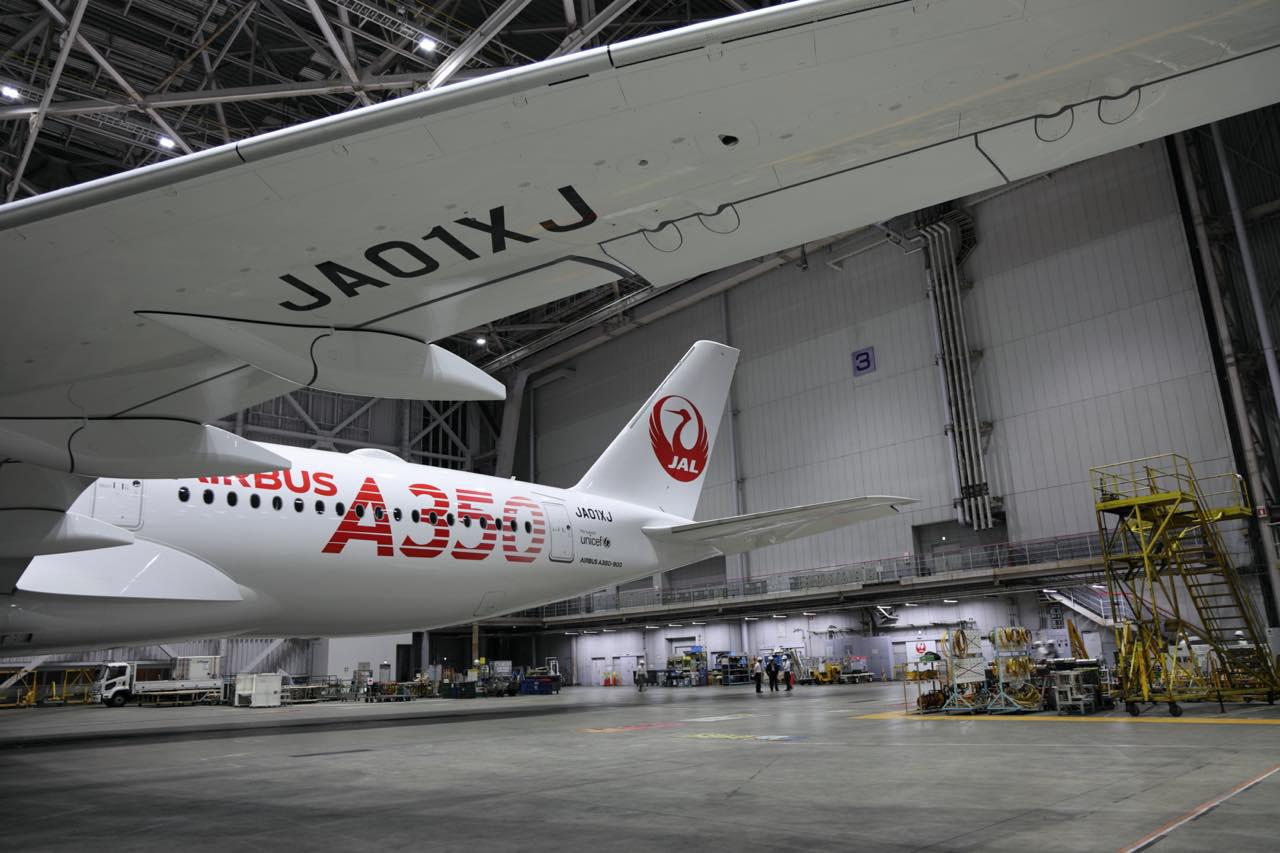
Abe: "I could tell how difficult it was, but in the end, it seemed like the teamwork was very effective."
The thing that got the biggest reaction from customers was the cockpit training flight simulator, which we prepared as a surprise after the maintenance area. Co-pilot Shinichiro Obata, who participated in this interview remotely because it was right after the flight to Amami, looks back on it.
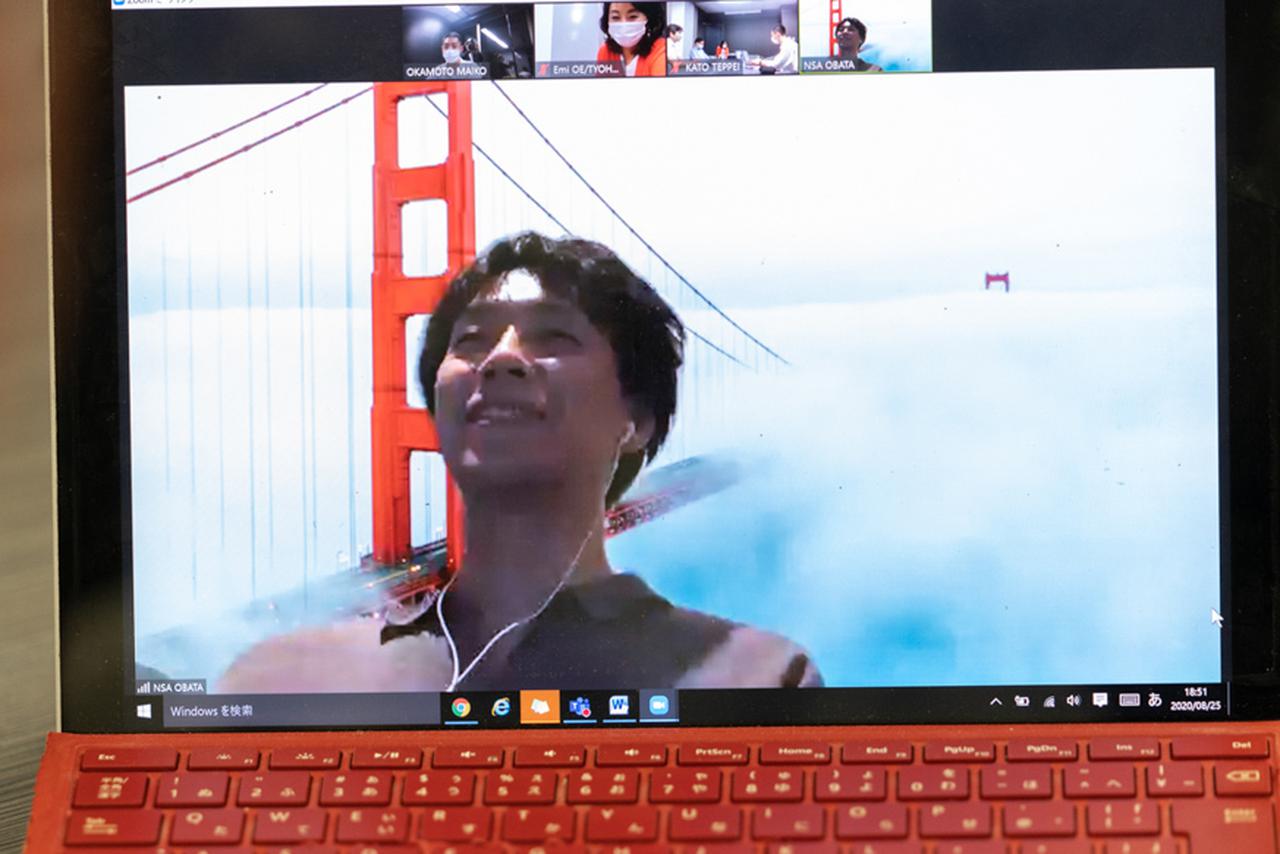
Obata: "Normally, you can't see inside the cockpit, so it's an unknown part for our customers. I thought that they would be happy if we included a flight simulator in the factory tour program, so I wanted to participate in this project."
The crew boarded a Boeing 767 training flight simulator and watched as a capsule-shaped enclosure moved back and forth and side to side using a hydraulic mechanism, providing a glimpse of full-scale training.
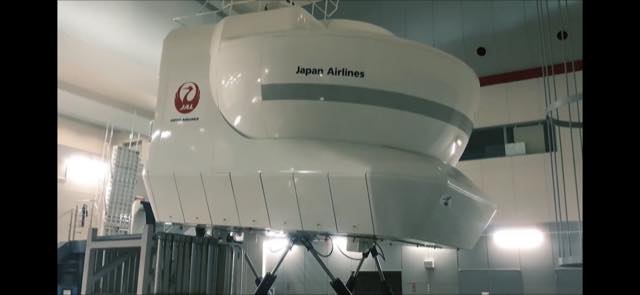
Obata: "The flight was performed by the captain and co-pilot in charge of the department conducting the verification. I think there are many things going on behind the scenes that our customers can see, such as the cabin crew and maintenance, so I would like to continue thinking about these things in the future."
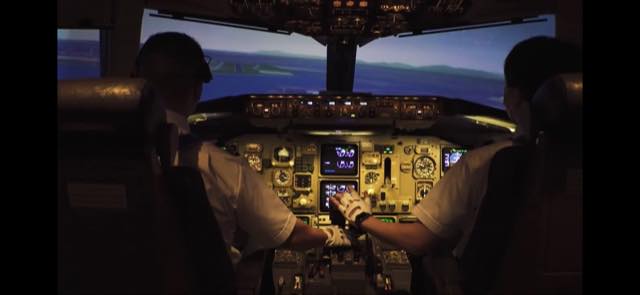
Taniuchi: "There was a huge response in the comments section. I ad-libbed an in-flight announcement saying, 'Welcome to our remote factory tour,' and it seemed to really resonate with the adult passengers. I'm really glad that Mr. Obata didn't give up and made it happen."
"popIn Aladdin" is also one of the partner companies that cooperated with this project. You can enjoy the factory tour on a large screen using a ceiling light with a projector provided by the company, making the images even more impressive.
Providing even more satisfying experiences for customers through remote work
The distribution was thus completed without any problems, with an estimated 13,000 people from 10 countries around the world accessing the video. A survey conducted after the distribution showed that most people were satisfied and would recommend the video to others.
Taniuchi: "We were a little unfamiliar with the process, but we were grateful to hear people say that it was good that it had a handmade feel to it. It was a big hurdle to get other departments involved, but there was not a single person who said that we didn't need to do this project. The project progressed in a positive atmosphere, and we were able to notice a big need. So we started streaming videos of the simulator that we recorded this time. We hope to be able to hold live remote participation programs several times a year in the future."
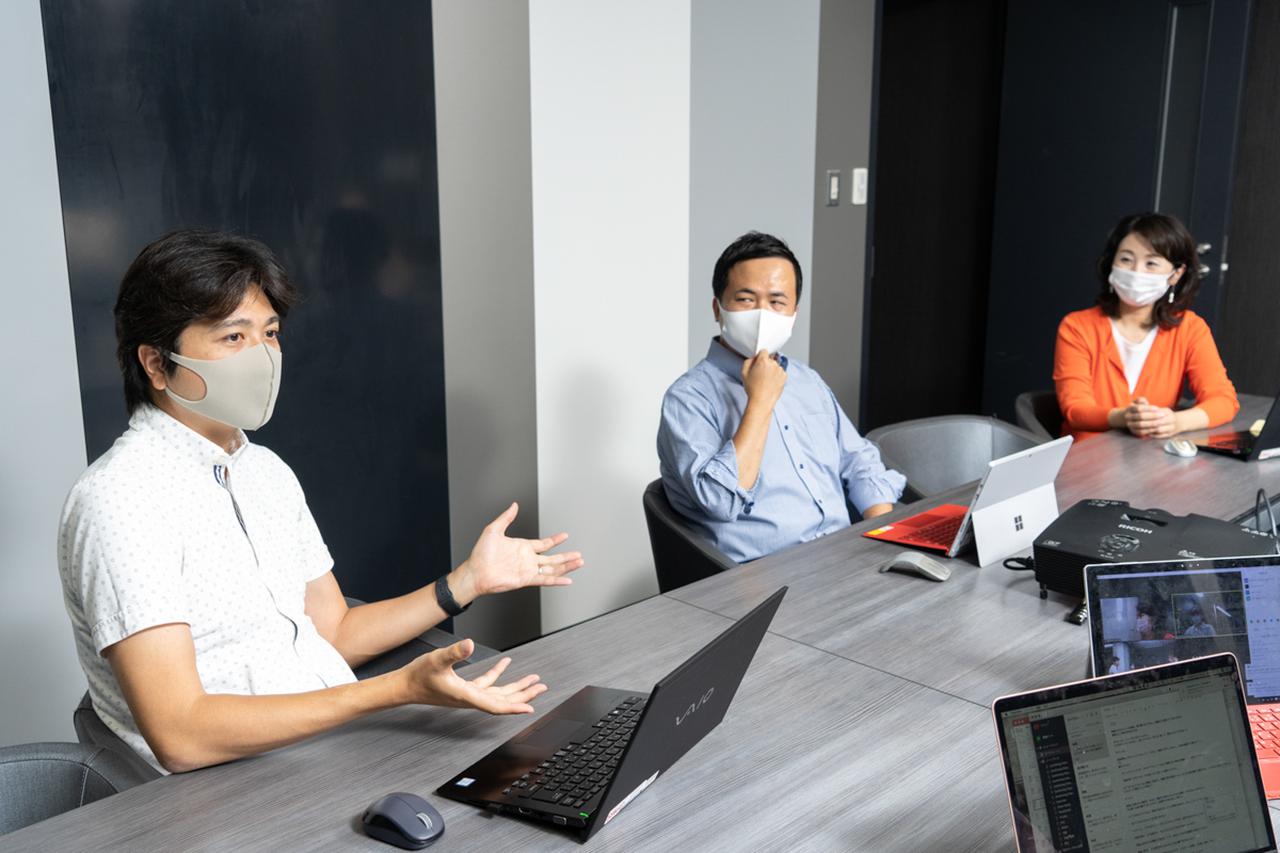
I think there is a lot of potential for content that can be created within a remote framework. Normally, for safety reasons, elementary school students and younger are not allowed to participate in factory tours, but this time, many children were able to come and visit, and some people even participated from places where it is difficult to go outside, such as hospital rooms.
Abe: "It was an initiative that had social significance and was well-received by all the participating staff. We think that we can use this framework to hold an online event that can connect the feelings of our customers, us, and the tourist destinations."
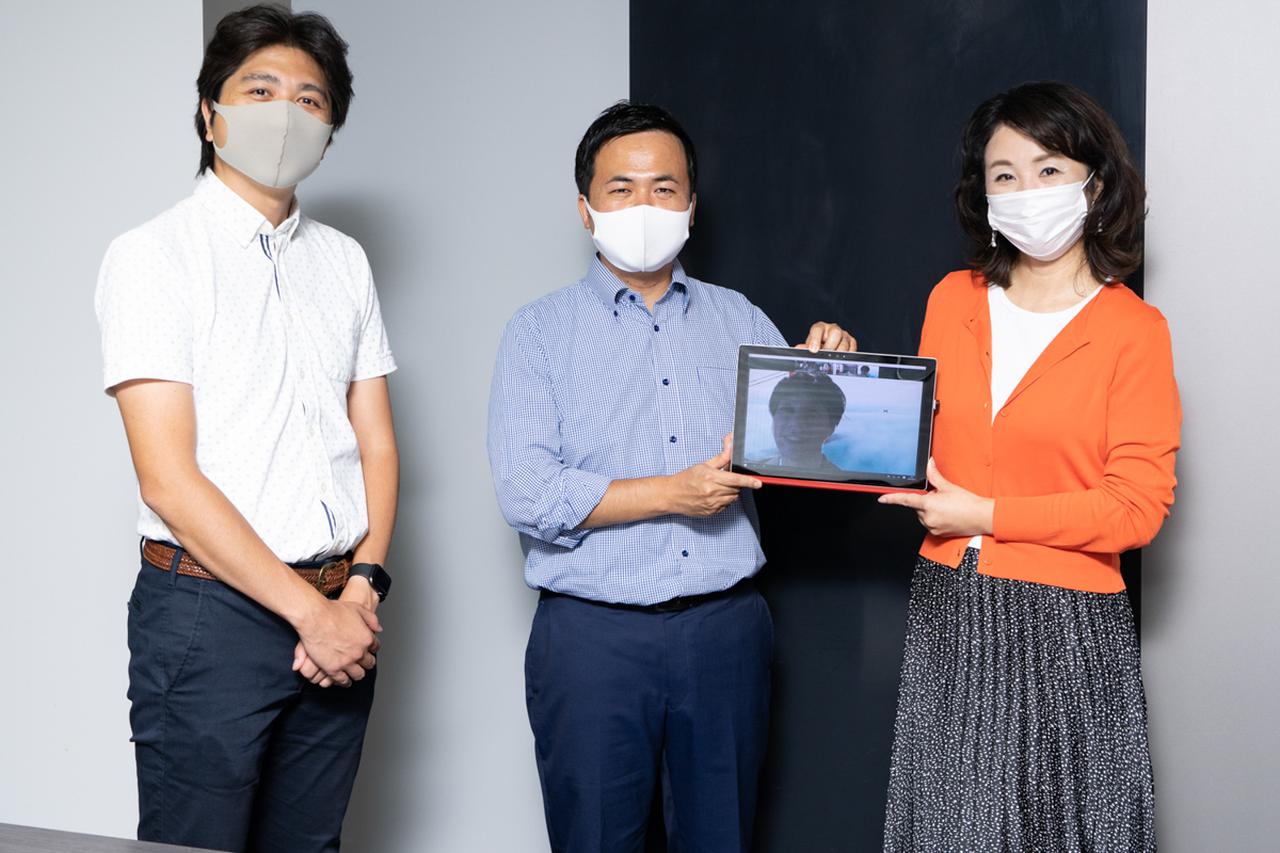
Even though the number of flights has decreased due to the COVID-19 pandemic, our staff continues to work tirelessly behind the scenes to maintain the safety of our planes and to continue providing high-quality service to our customers. Even if we can't board an airplane, we want to deliver something to our customers. This remote field trip, which started with that thought in mind, gives us a sense of the various possibilities for how we can enjoy airplanes in the future.
We'll take you behind the scenes of JAL's work, including inside stories on the introduction of the A350 and the development of in-flight meal menus.
The contents published are accurate at the time of publication and are subject to change.